Neue Umformtechnologie spart Rohstoffe Dienstag, 6. Dezember 2011
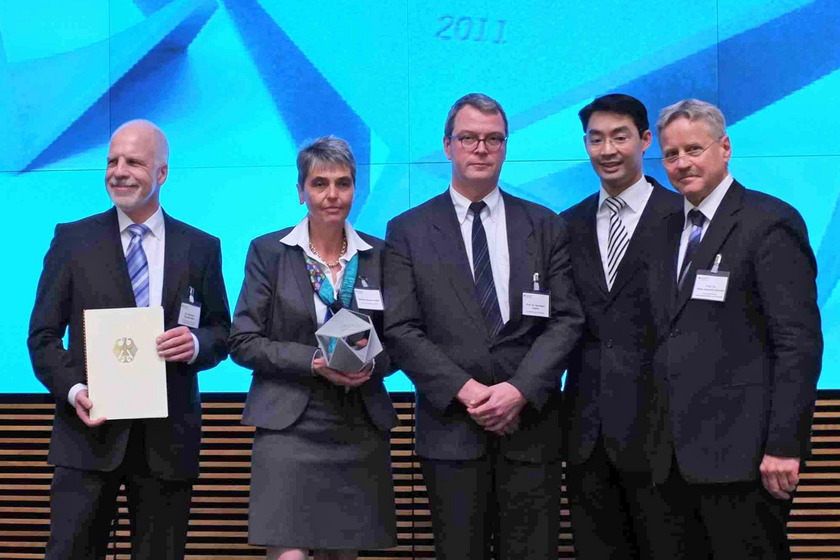
Deutscher Rohstoffeffizienz-Preis 2011 für Osnabrücker Labor für Umformtechnik und Werkzeugmaschinen
Im effizienten Umgang mit Rohstoffen und Material liegt großes wirtschaftliches Potenzial. Deshalb lobt das Bundesministerium für Wirtschaft und Technologie den „Deutschen Rohstoffeffizienz-Preis“ aus, mit dem soeben die Firma IFUTEC ausgezeichnet wurde. Das Ingenieurbüro für Umformtechnik aus Karlsbad arbeitet seit acht Jahren eng mit dem Labor für Umformtechnik und Werkzeugmaschinen der Hochschule Osnabrück (LUW) zusammen. „Teile der für die Preisverleihung relevanten neuen Umformtechnologien wurden auf Basis eines europaweit erteilten Patentes durchgeführt, das gemeinsam von der Hochschule Osnabrück und IFUTEC gehalten wird“, sagt der Osnabrücker Professor Dr.-Ing. Bernhard Adams.
Die insgesamt vier Preise über jeweils 10.000 Euro zeichnen herausragende Unternehmensbeispiele für rohstoff- und materialeffiziente Produkte, Prozesse oder Dienstleistungen sowie anwendungsorientierte Forschungsergebnisse aus. "Die Preisträger sind eindrucksvolle Beispiele dafür, wie Wirtschaft und Wissenschaft gemeinsam neue Lösungen zum nachhaltigen Rohstoffeinsatz finden“, erklärte Bundesminister Philipp Rösler während der Preisverleihung am 30. November in Berlin und verwies auf die wissenschaftliche Unterstützung des ausgezeichneten Unternehmens durch das LUW.
Ausgezeichnet wurde ein neues Verfahren der Achsenherstellung von Motorrädern, das inzwischen jährlich 130.000 kg Rohmaterial einspart. Herkömmlicherweise entstehen bei der Herstellung von vielen Metallteilen Späne, die aufwändig gereinigt und recycelt werden müssen. Diese Materialverschwendung kostete zum Beispiel den Zulieferer von BMW-Motorrädern in der Achsenproduktion 200.000 Euro pro Jahr. IFUTEC entwickelte deswegen ein anderes Verfahren: Statt ein dickwandiges Rohr zu zerspanen, wird die Achswelle in einem partiellen Warmumformverfahren aus einem dünnwandigen Rohr hergestellt. Dieses wird mit spezieller Werkzeugtechnik im Mittelbereich gestaucht und erhält so einen spanlos und faltenfrei ausgeformten Mittenbund.
Der effiziente Technologietransfer hat bereits Geschichte: Im Rahmen der gemeinsamen Forschungsarbeiten auf dem Gebiet der Metallumformung mit IFUTEC wurde Professor Adams bereits vor zwei Jahren mit dem Konrad Albert Schäfer-Preis der Konrad Schäfer Stiftung ausgezeichnet.
Von: Dr. Viola Düwert